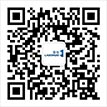
2020 官网升级中!现在您访问官网的浏览器设备分辨率宽度低于1280px请使用高分辨率宽度访问。
Professor Yang Yongqiang, a domestic metal 3D printing expert
The laser beam, which can make the material reach temperatures of more than 1,000 degrees Celsius, instantly melts the metal powder and makes it quickly solidify. Controlled by a computer program, the melting and solidification process is repeated with dizzying rapidity — gradually forming a precise artificial bone implant.
In Guangzhou 3D Printing Industrial Park, the first national 3D printing incubator in China, Professor Yang Yongqiang from South China University of Technology watches the debugging process of a metal 3D printer in his workshop.
With the unremitting efforts of the technical backbone led by Him, the first batch of 18 metal 3D printers have been produced and are being debugged. On weekdays and weekends, whenever he is free, Yang Yongqiang will come to the 3D industrial park to discuss with the backbone of enterprises how to further improve the metal 3D printer technology. As a leader of metal 3D printing in China, he hopes to industrialize metal 3D printing as soon as possible, and this road has been ten years for him.
Professor and doctoral supervisor of South China University of Technology
In 1982, 1987 and 1993, he received his bachelor’s, master’s and doctor’s degrees from the Department of Mechanics, Tianjin University. The Chinese mechanical engineering society of increasing material manufacturing and design of branch of director, vice director of China 3 d printing, material manufacturing (3 d printing), guangdong province association, director of the 3 d printing standardization committee of guangdong province, guangdong province industry association secretary-general, the laser association (LIA), a senior member, etc.
Professor Yang yongqiang has done a lot of research work in additive manufacturing (3D printing), laser material processing, welding equipment and technology, and successfully developed the first laser selective melting (SLM) rapid forming machine in China, realizing the direct rapid forming and manufacturing of metal parts. And the metal 3D printing technology featuring digitization, networking, personalization and customization is applied in the medical field.
Since 2013, it has undertaken more than 30 projects including international cooperation projects of the Ministry of Science and Technology, National Natural Science Foundation of China and major special projects of Guangdong Province. He has published more than 260 academic papers and more than 150 SCI papers. 44 invention patents and more than 100 utility model patents have been authorized in China, the United States and Germany.
Metal 3D Printing team
The technology is in a leading position in China
Metal A metal object printed by a 3D printer
In front of Yang Yongqiang’s eyes, a metal 3D printer is working fast. The three cubic centimeter model was virtually “sliced” into 1,000 layers by a machine computer.
“Our printing accuracy is so high that it only takes two hours to print.” That statistic makes Yang proud. The machine, he says, works with precision measured in microns (thousandths of a millimetre) : it can shape complex parts from point to line, line to surface and surface to shape with precision as small as 20 microns.
“From metal crowns, fixed Bridges, implants to jewelry, special-shaped parts, aerospace accessories… All of them can be made using this metal 3D printer.” Yang yongqiang said that at present, the RESEARCH team of SCUT has provided medical equipment manufactured by 3D printing, including surgical guide plates, hip bone plates and other implants, to many clinical hospitals. It has successfully completed dozens of clinical trials and achieved breakthrough success, reducing the amount of surgery and speeding up the recovery of patients.
“3D printing is rapidly changing our traditional mode of production and way of life. As a technology that will change the world, 3D printing technology will drive a new round of scientific and technological revolution and industrial revolution. Enterprises and research institutions at home and abroad have used 3D printing technology not only to print parts of airplanes, missiles, satellites and manned spacecraft, but also engines, drones and miniature satellites.” Professor Yang Yongqiang told reporters.
If 3D printing is “a technology that is going to change the world”, then laser selective melting metal 3D printing is at the top of the “spire” of the 3D printing industry. South China University of Technology is the first scientific research institution in China to systematically study the equipment, process and application technology of laser selective melting metal 3D printing, and is known as the “Huangpu Military Academy” of metal 3D printing. Its academic leader, Professor Yang Yongqiang, led the team to develop the first laser selective melting metal 3D printer in China and the world’s first 3D printing products directly manufacturing orthodontic tongue side brackets, which sent metal 3D printing technology to the country and incubated a number of 3D printing equipment and application enterprises with market competitiveness.
The core team and technology of Guangzhou Lejia that Yang Yongqiang belongs to come from South China University of Technology. With years of technical accumulation in LaserAdd series of industrial metal 3D printers, the company has developed the world’s advanced high-precision metal 3D printers. Only one and a half years after it settled in the industrial park, Lejia Additive has developed 6 models of machines, and its sales are expected to exceed 10 million yuan in 2018. Its development speed is regarded as a myth in the industry.
“Our metal 3D printing technology team is leading in China.” Tsinghua University, Xi ‘an Jiaotong University and Huazhong University of Science and Technology are the sources of 3D printing technologies such as FDM, SLA and SLS in China, and have made outstanding contributions to China’s 3D printing technology industry, Yang told reporters. The reporter learned that with his foresight and unremitting efforts, Professor Yang yongqiang became the first and fourth technical team in China to systematically carry out research on SLM metal 3D printing equipment, process and application technology.
Led by Yang Yongqiang, the 3D printing tongue side bracket manufacturing method has obtained invention patents in Germany and the United States, leading the world, and obtained medical licenses in China, the United States, the European Union and Russia, realizing industrialization and generating huge economic benefits.
3D-printed metal pieces
Technology promotion has hit a wall
After ten years on the bench, breakthrough results were achieved
Innovation will never be accomplished overnight, and it will never be plain sailing from technology forming to industrialization. Yang yongqiang says he spent a decade on the sidelines developing and improving technology.
Thirty-one years ago, After Yang Yongqiang graduated from his master’s degree, he chose laser processing technology as the content and direction of his research work. “At that time, laser was a cutting-edge technology, China’s laser processing technology was still relatively backward, and there was a talent fault in the country. I am very optimistic about the development of this technology and have been doing research for more than ten years.”
“Since 2002, thanks to the accumulation of years of experience in the research of laser cladding surface modification technology, I had the idea of expanding the technology of single-layer cladding to multi-layer stacking molding, so I started the exploration of laser selective melting technology for powder laying.
He said that the technological progress and achievements of the metal 3D printing industry cannot be separated from the support of the government and universities.
With the dream of manufacturing power, Yang Yongqiang began to prepare for the research of laser selective melting rapid prototyping technology in September 2002, but was at a loss for lack of funds.
At that time, metal 3D printers were monopolized by foreign giants with a price of 5 million yuan per machine. When he was troubled by this, the scientific research funds of the government and school helped Yang Yongqiang a lot. When raising funds, guangdong Provincial Department of Science and Technology gave him 200,000 yuan of special funds for scientific and technological research, and South China University of Technology gave him 200,000 yuan of funds for seedling project. The 400,000 yuan became Yang yongqiang’s initial capital to develop metal 3D printers.
Soon after, Yang found a Beijing-based company he wanted to partner with to help him assemble a metal 3D printing device he had designed by sharing technology and starting up with 400,000 yuan. The company took out a discarded old equipment for transformation, and Yang Yongqiang took out 400,000 yuan of scientific research funds to purchase key core components. In April 2004, the first laser selective melting rapid forming machine was finally born in China.
With the first metal 3D printer, Yang yongqiang started industrialization.
In August 2004, Yang Yongqiang came to Chang ‘an, Dongguan, to promote 3D printing in local professional towns one by one. But reality threw him a wet blanket.
“At that time, our technology was limited, the software and hardware were not mature, and the mold industry manufacturers did not recognize them. They compared the advantages of CNC machine tools with the disadvantages of metal 3D printing: the size accuracy was not enough, the surface accuracy was not high, and even the density and strength of printed metal parts were not high enough.” However, Yang yongqiang did not give up and still devoted himself to studying the application of metal 3D printing in other industries: “Even if it is not on the bench, I will stay there. I wasn’t afraid to sit here for a few more years, but it turned out to be ten.”
In the past ten years, Yang Yongqiang has never stopped his research on metal 3D printing technology. After 2005, optical fiber laser began to be applied to 3D printing equipment in foreign countries. At the same time, Yang Yongqiang also obtained the support of guangdong-Hong Kong bidding project of Guangzhou Science and Technology Bureau (Science and Technology Innovation Commission), purchased 200W optical fiber laser at the price of more than 400,000 yuan at that time, and developed dimetal-280, a metal 3D printing equipment with optical fiber laser as the light source. In 2007, he launched the Dimatal series of metal 3D printers considering the combination of industrialization with medical and jewelry industries. Since 2012, the company has cooperated with The Third Hospital of Peking University to conduct research on 3D printing technology of personalized knee prosthesis, which has achieved breakthrough results and authorized more than 20 patents. It is expected to obtain the third-class medical device license in the next 1-2 years, and promote and apply in the third Hospital of Peking University and other hospitals.
In 2012, the 3D printing industry finally ushered in the big development period of the industry. “The rapid development, especially from 2015 to 2016, 3D printing enterprises were everywhere. The scale of metal 3D printing began to develop rapidly with the application of industry and stomatology, with an annual growth rate of 20% to 30%.”
According to the annual Report released by Wholers Report, an American research firm specializing in 3D printing industry, only over 1,700 metal 3D printers were sold globally in 2017. Buyers are mainly concentrated in universities, scientific research institutions, medical institutions and so on. “3D printing started only 30 years ago, especially in the field of metal 3D printing, in the next 10 years will be in a period of rapid growth. At present, we are on the same starting line with the world giants, and can run and even lead the giants.” Yang yongqiang said.
Carry forward the national spirit – the spirit of struggle
He likes to talk about his achievements as a “team”
Although he is a leader in metal 3D printing, Yang yongqiang seldom talks about himself. He always says: “We are a team, and it is the crystallization of the collective strength of the team.” In the past 16 years, the metal 3D printing team of SOUTH China University of Technology has applied for more than 260 patents, including 40 authorized invention patents, 99 utility model patents, and a number of software copyright and appearance patents. It is the team with the most intellectual property rights and the most complete layout in the field of metal 3D printing in China. “Everyone says that China Institute of Technology can be regarded as the ‘Whampoa Military Academy’ in China’s METAL 3D printing industry, and many leading domestic enterprises have their technology sources here.” Yang yongqiang said.
For the base
Promote the upgrading of the local medical device industry
According to the annual Report released by Wholers Report, a US company specializing in 3D printing industry research, the global 3D printing market will reach 12.5 billion US dollars by 2018, quadrupling that of 2014.
Looking to the future, with the gradual improvement of the technical system, the accelerated expansion of application fields and the continuous formation of the industrial chain, the global 3D printing market may further usher in explosive growth.
On November 30, 2017, the Ministry of Industry and Information Technology and National Development and Reform Commission, the Ministry of Education, Ministry of Public Security, Ministry of Finance, the Ministry of Commerce, the ministry of culture, the national health and family planning commission, state-owned assets supervision and administration commission, the General Administration of Customs, quality supervision, inspection and quarantine, and intellectual property office of the twelve departments issued about print and distribute “add material manufacture industry development action plan (2017-2020)”, according to the plan, By 2020, the annual sales revenue of additive manufacturing industry will exceed 20 billion yuan, with an average annual growth rate of more than 30%.
Guangdong is at the forefront of reform and opening up. Guangdong province and Guangzhou are among the most supportive of 3D printing industry in China, boosting the development of metal 3D printing. In Guangzhou, leading entrepreneurial teams can receive up to 30 million yuan in support, according to the report.
According to the Implementation Plan for Accelerating the Development of 3D Printing Technology and Application Industry in Guangdong Province, Guangdong province has invested more than 150 million yuan in major special projects of Guangdong Province — 3D printing for three consecutive years from 2014 to 2016, and will continue to maintain support from 2017 to 2018. At present, China is promoting the local medical device industry to gradually move to the upstream of the value chain high-end medical device field through cost advantage and technology improvement. The development level of guangdong province in the field of medical devices has always been in the forefront in China, and there will be great development space in the future in the medical market of 3D printing, especially in orthopedic implants.