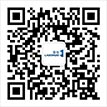
官方微信
2020 官网升级中!现在您访问官网的浏览器设备分辨率宽度低于1280px请使用高分辨率宽度访问。
为何选择3D打印
3D打印制造技术在医疗健康领域的优势主要体现在以下几个方面[1]。
材料及应用
医疗器械需满足一定的尺寸精度、机械性能、生物兼容性(国际标准ISO-10993)、耐腐蚀。如下图所示,医用植入物可用于颅骨、下颌骨、肩胛骨、胸骨、脊柱、髋骨、膝关节和截骨相关的手术。用于3D打印的金属材料主要为钛和钛合金,钽,医用不锈钢,采用粉床激光或电子束选区熔覆工艺[2]。
从复杂的面部整形手术到骨科和创伤外科手术,例如颅骨的修复、下颚骨的整形,植入物的几何形状通常非常复杂。在患者安全和满意度、医院效率和经济效益方面,3D打印的植入物可以提供更好、更可预测的结果,比如提高手术成功率,降低需二次手术的可能性。
脊柱植入物被用来恢复患者的椎间高度。这类医疗器械通过轻量化的晶格结构设计来模仿骨骼机械特性,这里特指部件的弹性模量。传统的制造技术无法生产出具有晶格结构的脊柱植入物,而晶格结构具有较高的表面积,可促进成骨细胞向植入物迁移,并能优化多孔体的机械性能,以满足所需的加载条件。
3D打印颅骨、下颌骨、肩胛骨、胸骨、脊柱、髋骨、膝关节、截骨。图源:[3]
图源:雷尼绍
工艺流程
通过结合X射线扫描、CT、核磁共振成像或超声波扫描等技术获得生物结构的医学影像,3D打印技术可为每一位病例制造专用的植入物,其解剖结构几乎与受伤组织相同。
针对3D打印植入物的常见后处理工艺有除粉,应力消除热处理,去支撑,喷砂,磨料流抛光以及用来去除经喷砂和磨流抛光后留在表面的碎片以及因部分熔化而粘结在表面的粉末颗粒的电解抛光[4]。在抛光过程中,通常会使用一些强腐蚀性的溶剂,比如用于外科植入式不锈钢装置的磷酸和硫酸混合液(ASTM A380)。最后,用去离子水清洗部件,干燥。
在某些应用中,表面改性的技术比如微弧氧化和表面涂层也被运用到3D打印的支架上。热处理可以改善部件的表面粗糙度,有助于矿物质的富集,细胞的附着和生长。
标准与认证
尽管已经有许多临床试验使用定制化植入物,然而,由于缺乏相关法规或法律的指导,3D打印在医疗植入物领域的发展可能会受到阻碍。
首先,医疗器械的生产需要满足质量管理体系的认证要求,比如针对定制化植入物的国际标准ISO13485。在销售或分销前,制造商必须向目标市场所在的国家或地区注册意向销售的医疗器械,如中国的NMPA,欧盟的MDR以及美国的FDA。这些机构为制造商提供建议,其中包括3D打印医疗设备开发过程中的设备设计、制造和测试注意事项等。为了确保产品的性能,制造或者服务的可重复性以及可追溯性,地区机构会对制造商内部建立的质量管理体系进行审核。
因为3D打印的整个工作流程始于从医学影像到数字模型和加工文件的建立,玛瑞斯率先对其设计软件产品和切片等流程进行了认证,确保加工文件和实际生物结构相一致。为了确保.stl文件和构建文件中部件几何尺寸的精度(具体工作流程如下图所示),玛瑞斯建立了可靠的数据库。
此外,玛瑞斯的团队会定期通过文献调研来了解用户如何运用软件开展不同的研究,并从中来找到软件中影响切片准确性的弱点。玛瑞斯在全球拥有广大的客户群体,可以更有效地对软件实现迭代升级,提高其稳定性。
切片软件的验证流程以及医学影像(左),数字模型(中)和两者尺寸差(右)的对比,图源:玛瑞斯
官方微信